Recently installed these on my '06, hoping to fix a slight misfire when the vehicle reached operating temperature. If you look at the rusty bolt at the top left of the picture, water seemed to be pooling there and running into the ignition coil "bay" underneath the cover. You could see the residue from the leak inside the bay. It had gotten into the 4th and 2nd plug well, oddly skipping the 3rd in between (either from boot degradation on the infiltrated wells, or from a recent replacement). They were really rusty, and the old coil boots were more orange than black.
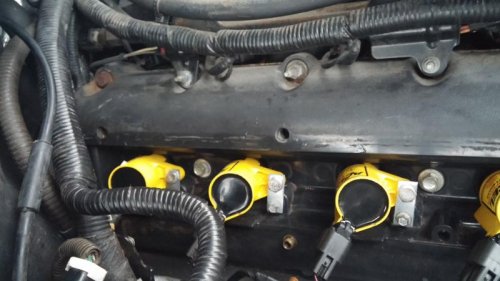
I bought some stainless steel corner brackets (set of 4 for about $2.50) and just cut the corners out. Leaving me with 8 well sized COP brackets; the space you need between the two holes is about 2 cm. I used some tubing, like the kind you get for washer fluid line, under the bracket to keep tension on that 7mm bolt since there will be a gap there. Although this way is probably a little tighter, if I had to do this again I'd suggest PM'ing Hite337 for his fabricated ones.The Accel coil fittings were pretty easy to tap for a regular stainless steel screw, hand-tightened with some loctite (didn't want to use too much force there).
I really think people considering these should try and use the boots that came on the Accels, they seal the plug wells very satisfyingly. Orientation of the Accels comes into play here in order to get them to make good contact with the spark plug. You'll have to contend with the bump underneath the electrical connector (you can see it sticking out on the far right of the above picture) and the intended mounting bracket. The driver side (not pictured) coils are rotated 90 deg clockwise in order to fit in the same way, yes the connectors wont be orientated the same on both sides. It doesn't look cosmetically perfect, but hey, it gets the job done.
After mauling my first connector, I had a few ideas that may make it easier for future attempts.
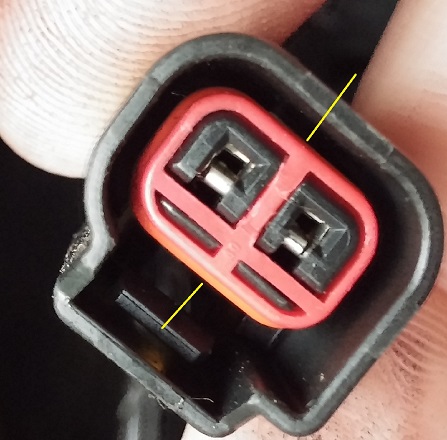
1. I wouldn't suggest using anything like a regular flat screwdriver. The force it applies to the red plastic piece is just too spread out. Instead use two small instruments, like jewelers/mini flat head screwdrivers, right were the two yellow lines are. This is a bulky area of plastic that is less liable to breakage.
2. Having another set of hands is tremendously helpful.
3. Like others said it doesn't come out all the way, but enough to grab it with something. Stop your prying and use surgical style forceps if you have them, or needle nose pliers to pull it out the rest of the way.
4. To depress the detent to remove the wiring, you don't need much force just well placed or you'll break more plastic. I found it easier to push on the fat, curved section of the wiring ends to back it out of the connector with my small screwdriver, rather than pulling the wire out the back.
Its not hard to do, just take your time. I hope this helps people for future installs.
Some questions for people who have done this:
Did anyone else not have connectors "click" into the Accel COPs? I had about half of them just fit on with friction. After a drive I checked them and all but one is now properly locked on to the COP (weird, heat expansion?). I'm wondering if the little red gasket in the connector on that one is twisted or something.
I'd like to track down that water leak on the passenger side. The hood seal seems great, almost new. I'm thinking the plastic cowl that goes under the wipers and over cabin air box is suspect. It seems to be leaking right where the low point on that seal to the windshield is. Tests were inconclusive, but I couldn't really replicate hours of rainfall. Can anyone confirm this as a problem area?